Dental 3D Printing: The Importance of UV Curing Ovens
By Dr. Luis De Bellis
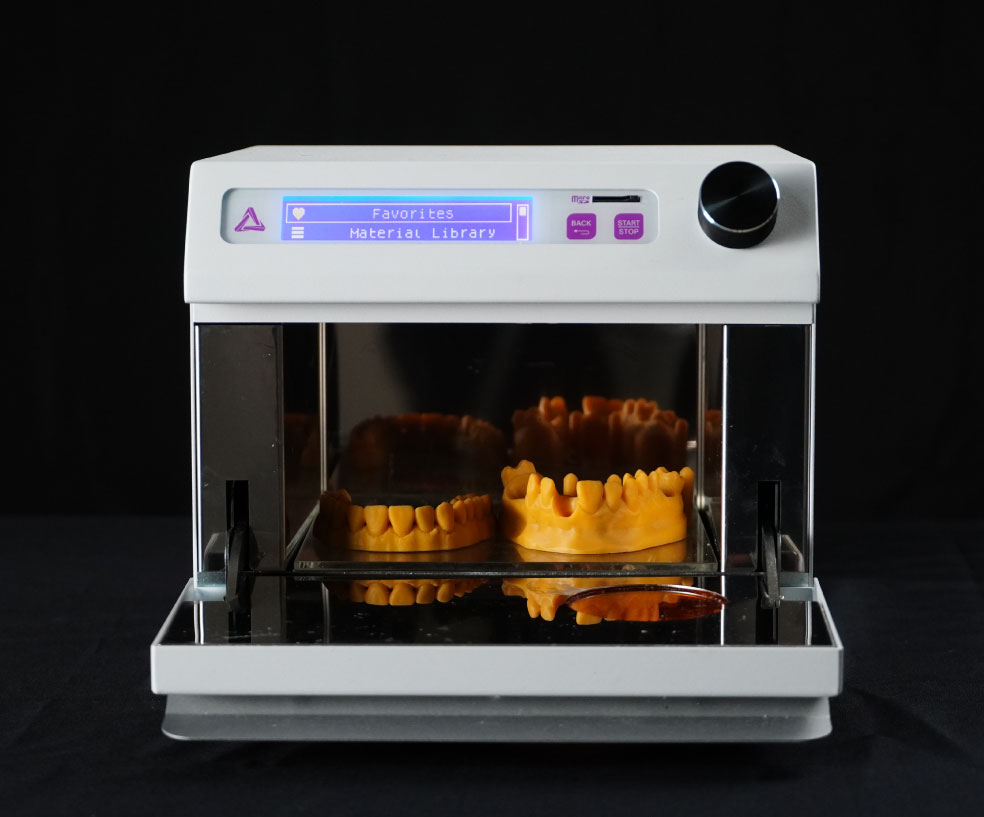
Venturing into the 3D Printing World
Starting out as a dental technician in 2001 and studying dentistry at a later stage has given me a significant advantage in implantology and employing high tech in my work - I understand the manufacturing processes and learned how digital tools can make my work more efficient early on.
During my postgraduate studies in implantology, I discovered the 3D printing world. While the course covered some details about additive manufacturing, it was too generic to make use of it right away. But it caught my attention & I knew this was the future of medicine.
Consequently, I bought an extrusion 3D printer, which I used to learn about this printing modality. It also helped me to learn how to transform DICOM files into STL and be able to achieve 3D models with smooth surfaces.
After about a year of using it, I bought a kit to build a cartesian laser printer. However, it was a real disaster due to the sheer amount of moving parts involved. Nonetheless, this experience was the nudge I needed to build my first DLP printer with a projector.
Wisdom comes from experience
I am currently developing my skills with bioprinter and bioinks, used to print functional tissues. Through this journey, I discovered a similarity to what I first experienced when making my first impressions with resin - the role post-processing plays for the printed parts.
Generally speaking, many people dedicated to 3D printing do not give enough importance to the impact that the post-processing of the manufactured part will have. It is critical to highlight that post-processing helps us obtain more resistant pieces and contributes to applications that will not be cytotoxic. In other words, we will be able to guarantee to comply with international health standards.
It is worth noting that not all curing units are the same. Unfortunately, more often than not, we can find many enthusiasts using nail ovens to post-process 3d printed parts. These ovens do not fall within any specific classification. Therefore are unable to achieve uniform post-polymerization. Consequently, the risk of obtaining a piece with unintended physical and chemical characteristics will be extremely high.
The world of dental Post-Processing
When it comes to dental applications, we can find class I and class II UV curing units. The difference lies in the kind of resins that each can polymerize and the time that said polymerized pieces can be used intraorally.
Class I units can be used to cure prints that patients will not use intraorally for over 30 days (such as surgical guides, indirect bonding trays, and dental models). On the other hand, Class IIb units can also cure applications meant to stay in the patient's mouth over a long period (such as splints, dentures, and temporary crowns).
UV curing units that do not have any classification should only be used for 3D prints that require no classifications, i.e. dental models and gingiva prints to indicate the placement of restorations.
Among these UV curing ovens, we can find differences in quality and price. You can experience noticeable contrast among such equipment with everyday use.
3D printing resins include multiple photoinitiators which react with the UV light emitted by the UV curing unit.
With a mix matrix UV curing unit, a higher degree of conversion can be achieved leading to improved mechanical properties of the 3D printed part. A mix matrix is not common in the most basic curing units, which often employ a light column of a single UV wavelength, a disadvantage considering the penetration power of the radiation will not be enough. Consequently, we will obtain a piece with diminished physical and chemical characteristics.
360 degree light distribution of advanced and specialized dental UV curing ovens add to further in-depth curing versus curing units which have only one light column installed. Technicians or clinicians using cheaper units with single light columns will need to manually rotate the object and it’s unlikely to be approved for biocompatible 3D printing in dentistry, as no uniformity can be achieved.
Moreover, these units do not have temperature control inside the post-curing chamber. Although this factor is generally not considered by many, it will become vital when performing physical and chemical tests. To provide contrast, we can find equipment with a strategically arranged radiation source among the higher-priced post-curing units. It allows us to obtain a uniform incidence of radiation on the printed piece. As a result, we get a final product with optimal characteristics that meet international health requirements.
Last but not least, we need to consider how the radiation is emitted from the light source. Medium and high-end units come with flash-type radiation sources. Because the amount of radiation and the temperature inside the post-curing chamber can be perfectly controlled, we obtain a great benefit when carrying out the post-curing cycles.
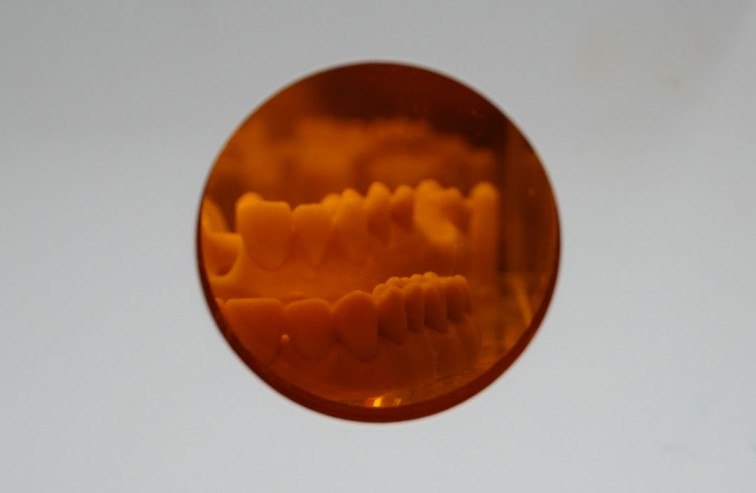
Validated Printing Workflows
When looking back at the research of the past decade, it’s become clear that post-processing is a vital step in 3D printing biocompatible parts and to ensure that this step meets the requirements, quality assurance in the form of biocompatibility and mechanical property testing is required.
Companies that manufacture mid-range and high-end post-curing units usually work directly with the resin manufacturers to leave validated preset times in the memory of the post-curing units. It is not just a matter of convenience, but much more a matter of risk aversion - preset times mean that experts have taken their time to ensure the curing times will lead to biocompatible, safe and stable 3D printed applications.
Final thoughts
While there are more and more 3D printing systems in the market at various price points, I really appreciate the guaranteed quality that I have received from the Ackuretta ecosystems.
I can attest that these products are not only beautiful to look at but that they are also designed to deliver satisfaction in each action they perform. It translates into a more relaxed day–to–day because they are a true plug-and-play.
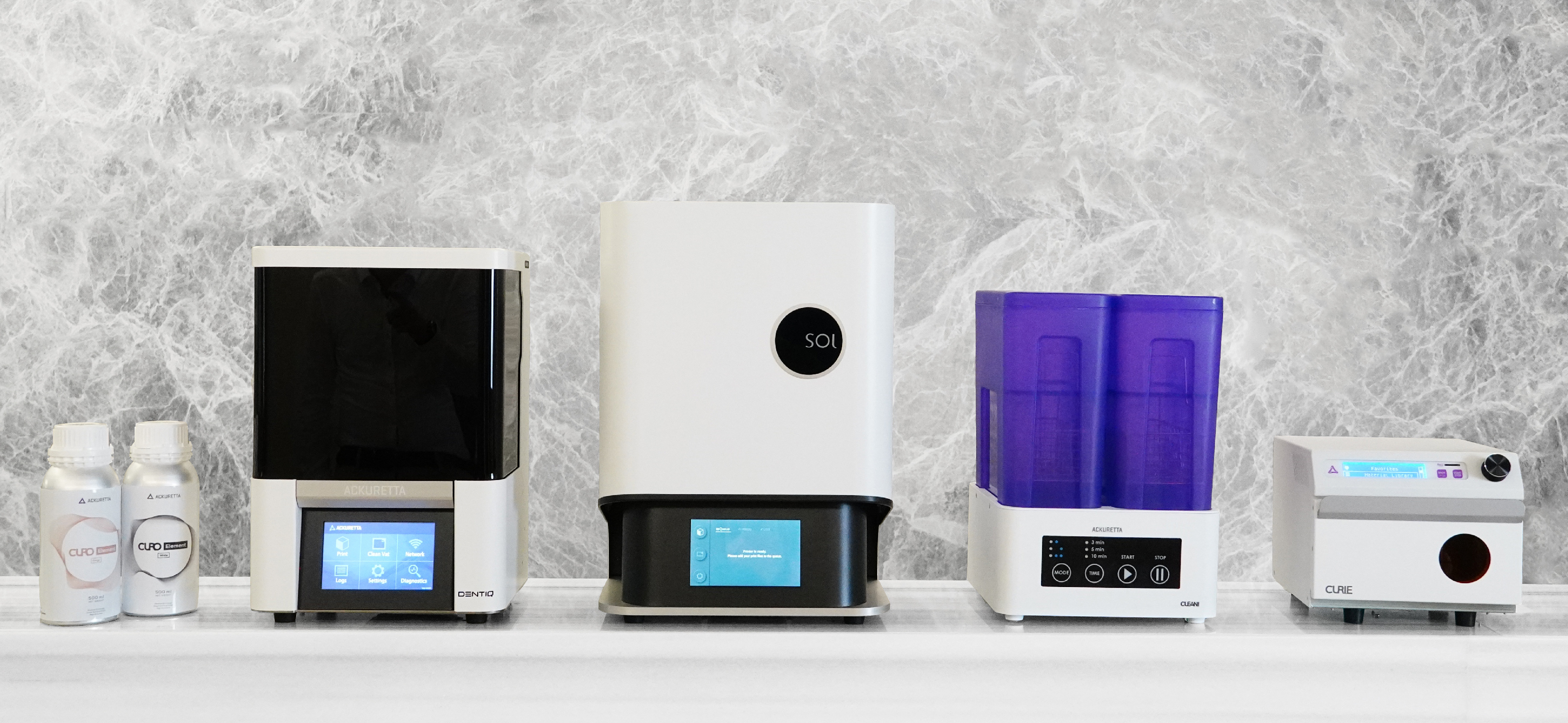
About the Author
Dr. Luis De Bellis
Dr. Luis De Bellis works as an adjunct professor at the Faculty of Dentistry of the University of Chile, as the third-year coordinator of the Oral and Maxillofacial Implantology Postgraduate program.
Starting out in the dental world in 2001, as an dental technician, Dr. De Bellis quickly learned about the different techniques to manufacture an array of dental applications, which inspired him to delve deeper into this exciting career. Later he studied dentistry and specialized in oral and maxillofacial implantology.